Badanie odporności korozyjnej AASS – klucz do trwałości konstrukcji
Korozja to jeden z najgroźniejszych wrogów konstrukcji metalowych, który może prowadzić do katastrofalnych awarii i ogromnych strat finansowych. W świecie, gdzie trwałość i bezpieczeństwo konstrukcji są priorytetem, badanie odporności korozyjnej AASS (Acetic Acid Salt Spray) staje się niezbędnym narzędziem oceny materiałów. Test AASS to zaawansowana metoda laboratoryjnego sprawdzania, jak materiały radzą sobie w ekstremalnie agresywnych warunkach korozyjnych. Dzięki temu badaniu inżynierowie mogą przewidzieć zachowanie konstrukcji w rzeczywistych warunkach eksploatacji i podjąć odpowiednie decyzje projektowe. Więcej informacji o procesach korozyjnych znajdziesz na https://tenslab.pl/korozja.
Współczesne budownictwo wymaga materiałów o wyjątkowej odporności na czynniki degradacyjne. Konstrukcje stalowe, aluminiowe czy z powłokami ochronnymi muszą wytrzymać lata eksploatacji w różnych warunkach atmosferycznych. Test AASS pozwala symulować te warunki w kontrolowanym środowisku laboratoryjnym, dostarczając cennych danych o przewidywanej żywotności materiałów.
Czym jest test AASS i dlaczego jest tak istotny
Test w kwaśnej mgle solnej AASS to jedna z najbardziej wymagających metod oceny odporności korozyjnej materiałów. Wykorzystuje roztwór chlorku sodu z dodatkiem kwasu octowego, który obniża pH do poziomu 3,1-3,3. Ta kombinacja tworzy wyjątkowo agresywne środowisko korozyjne, które przyspiesza procesy degradacji materiałów w porównaniu do naturalnych warunków atmosferycznych.
Specyfika testu AASS polega na jego selektywności. Nie wszystkie materiały nadają się do badania tą metodą. Ze względu na bardzo agresywne środowisko korozyjne podczas testu nie rekomenduje się badania metodą AASS stali, stali ocynkowanej oraz odlewów aluminiowych. Metoda ta jest szczególnie dedykowana dla materiałów o wysokiej odporności korozyjnej, takich jak aluminium architektoniczne czy próbki z powłokami dekoracyjnymi.
Wartość diagnostyczna tego testu wynika z możliwości przewidywania zachowania materiałów w ekstremalnych warunkach. Inżynierowie mogą dzięki temu optymalizować wybór materiałów już na etapie projektowania, co przekłada się na zwiększenie trwałości i bezpieczeństwa konstrukcji.
Metodologia i procedura badania AASS
Przeprowadzenie testu AASS wymaga specjalistycznego wyposażenia i ścisłego przestrzegania procedur określonych w normie PN-EN ISO 9227. Proces rozpoczyna się od przygotowania próbek, które muszą być odpowiednio oczyszczone i przygotowane zgodnie z wymaganiami normy.
Główne parametry testu obejmują:
- Temperatura komory testowej utrzymywana na poziomie 50°C
- Stężenie roztworu chlorku sodu wynoszące 5%
- Dodatek kwasu octowego obniżający pH do zakresu 3,1-3,3
- Kontrolowana wilgotność względna
- Równomierne rozpylanie mgły solnej
Podczas ekspozycji próbki są regularnie monitorowane pod kątem pojawiających się zmian korozyjnych. Ocena obejmuje analizę makroskopową na mikroskopie cyfrowym oraz analizę mikroskopową na mikroskopie metalograficznym. Czas ekspozycji może wynosić od kilkudziesięciu godzin do kilku tysięcy, w zależności od badanego materiału i wymagań konkretnej aplikacji.
Zastosowania testu AASS w różnych branżach
Przemysł motoryzacyjny szeroko wykorzystuje test AASS do oceny powłok ochronnych elementów karoserii. Producenci samochodów muszą zapewnić, że ich pojazdy wytrzymają lata eksploatacji w różnych warunkach klimatycznych, od słonych dróg zimą po wilgotne środowisko nadmorskie.
W budownictwie test AASS znajduje zastosowanie przy ocenie:
- Elementów fasad z aluminium architektonicznego
- Powłok ochronnych konstrukcji stalowych
- Materiałów wykończeniowych narażonych na agresywne warunki
- Elementów złącznych i mocowań
Przemysł lotniczy wykorzystuje tę metodę do certyfikacji materiałów stosowanych w konstrukcji samolotów. Elementy lotnicze muszą charakteryzować się wyjątkową trwałością, ponieważ awaria z powodu korozji może mieć katastrofalne skutki.
Branża morska i offshore szczególnie ceni test AASS ze względu na ekstremalne warunki eksploatacji w środowisku morskim. Konstrukcje platform wiertniczych, statków czy portów są narażone na ciągłe oddziaływanie słonej wody i agresywnej atmosfery.
Interpretacja wyników i ocena odporności korozyjnej
Analiza wyników testu AASS wymaga doświadczenia i znajomości specyfiki badanych materiałów. Ocena obejmuje identyfikację rodzaju korozji, jej intensywności oraz czasu do pojawienia się pierwszych objawów degradacji.
Główne kryteria oceny to:
- Czas do pojawienia się korozji czerwonej (dla materiałów żelaznych)
- Stopień degradacji powłoki ochronnej
- Rodzaj i rozmieszczenie produktów korozji
- Głębokość penetracji korozji
Wyniki testu AASS pozwalają na porównanie różnych materiałów i powłok ochronnych. Na przykład, badania wykazały, że powłoki cynkowo-magnezowe ZMg140 charakteryzują się wyjątkową odpornością – korozja czerwona rdzenia stalowego pojawiła się dopiero po 1008 godzinach ekspozycji w mgle solnej.
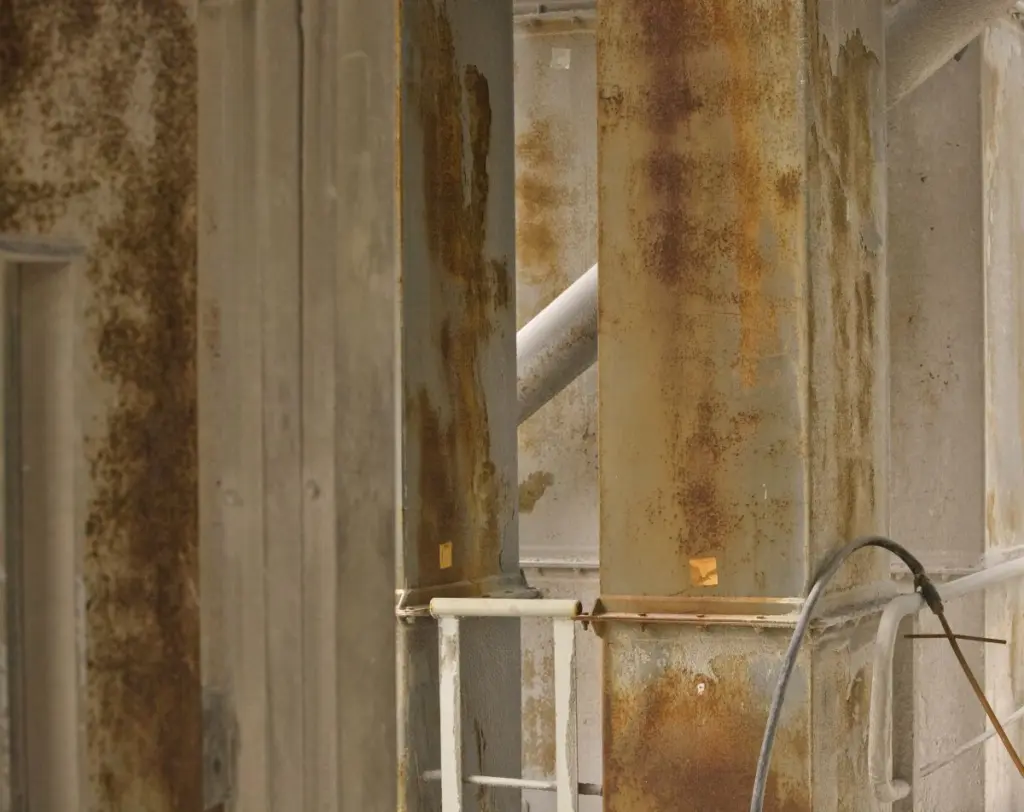
Interpretacja wyników musi uwzględniać specyfikę zastosowania materiału. Materiał, który nie przejdzie testu AASS, może nadal być odpowiedni do zastosowań w mniej agresywnych środowiskach.
Porównanie z innymi metodami testowania korozji
Test AASS stanowi część szerszego spektrum metod oceny odporności korozyjnej. Norma ISO 9227 obejmuje również test w neutralnej mgle solnej (NSS) oraz test w mgle solnej z dodatkiem miedzi (CASS).
Charakterystyka poszczególnych metod:
Metoda | pH roztworu | Temperatura | Zastosowanie |
---|---|---|---|
NSS | 6,5-7,2 | 35°C | Materiały podstawowe |
AASS | 3,1-3,3 | 50°C | Materiały odporne |
CASS | 3,1-3,3 | 50°C | Powłoki dekoracyjne |
Test NSS jest najmniej agresywny i nadaje się do oceny podstawowych materiałów konstrukcyjnych. AASS oferuje średni poziom agresywności, podczas gdy CASS jest najbardziej wymagający ze względu na dodatek chlorku miedzi jako przyspieszacza korozji.
Wybór odpowiedniej metody zależy od rodzaju badanego materiału i przewidywanych warunków eksploatacji. Często stosuje się kombinację różnych testów, aby uzyskać pełny obraz odporności korozyjnej materiału.
Wpływ składu chemicznego na wyniki testów
Skład chemiczny materiału ma decydujący wpływ na jego zachowanie podczas testu AASS. Szczególnie istotna jest zawartość pierwiastków stopowych, które mogą znacząco modyfikować odporność korozyjną.
W przypadku stali, zawartość krzemu w zakresie 0,03-0,12% mas. powoduje tzw. efekt Sandelina, który prowadzi do nadmiernego wzrostu grubości powłoki cynkowej i niepożądanej, gąbczastej struktury. Analiza chemiczna wykazała, że podłoże stalowe niektórych próbek należy do grupy stali reaktywnych z zakresu Sandelina, co wpływa na ich zachowanie podczas cynkowania.
Dodatki stopowe w powłokach ochronnych:
- Aluminium poprawia odporność na korozję atmosferyczną
- Magnez zwiększa skuteczność ochrony w obecności soli
- Nikiel zapewnia ochronę przed korozją wżerową
- Chrom tworzy stabilne warstwy pasywne
Największą zawartość magnezu (około 0,4% mas.) odnotowano w blachach z powłoką metaliczną ZMg140, co przekłada się na ich wyjątkową odporność korozyjną. Te powłoki uzyskały lepsze właściwości ochronne niż tradycyjne powłoki cynkowe przy znacznie mniejszej grubości.
Znaczenie badań dla bezpieczeństwa konstrukcji
Badania odporności korozyjnej metodą AASS mają bezpośredni wpływ na bezpieczeństwo użytkowników konstrukcji. Korozja może prowadzić do stopniowej degradacji właściwości mechanicznych materiałów, co w skrajnych przypadkach może skutkować awarią konstrukcji.
Korzyści z regularnych badań korozyjnych:
- Przewidywanie żywotności konstrukcji
- Optymalizacja harmonogramów konserwacji
- Redukcja kosztów eksploatacji
- Zwiększenie bezpieczeństwa użytkowników
Badania nieniszczące konstrukcji, w tym testy odporności korozyjnej, zaleca się wykonywać co najmniej 2 lata po oddaniu budynku do eksploatacji, a następnie minimum raz na 10 lat. Regularne monitorowanie stanu technicznego pozwala na wczesne wykrycie problemów i podjęcie odpowiednich działań naprawczych.
W przypadku konstrukcji narażonych na szczególnie agresywne warunki, takich jak obiekty w strefie nadmorskiej czy przemysłowej, częstotliwość badań powinna być większa. Proaktywne podejście do oceny stanu technicznego konstrukcji pozwala uniknąć kosztownych awarii i zapewnić bezpieczeństwo użytkowników.
Trendy i rozwój metod badawczych
Współczesne metody badania odporności korozyjnej ewoluują w kierunku większej precyzji i lepszego odwzorowania rzeczywistych warunków eksploatacji. Rozwój technologii pozwala na bardziej zaawansowane analizy procesów korozyjnych i lepsze przewidywanie zachowania materiałów.
Nowoczesne podejścia obejmują:
- Symulację cyklicznych zmian warunków atmosferycznych
- Zastosowanie technik elektrochemicznych do monitorowania procesów korozji
- Wykorzystanie sztucznej inteligencji do analizy wyników
- Rozwój nowych środowisk testowych lepiej odwzorowujących rzeczywiste warunki
Przyszłość badań korozyjnych zmierza w kierunku jeszcze bardziej precyzyjnych metod, które pozwolą na dokładniejsze przewidywanie zachowania materiałów w długoterminowej eksploatacji. Rozwój nowych materiałów kompozytowych i powłok ochronnych wymaga również dostosowania metod badawczych do ich specyficznych właściwości.
FAQ – Najczęściej zadawane pytania
Jak długo trwa test AASS?
Czas trwania testu AASS zależy od badanego materiału i wymagań specyfikacji. Może wynosić od kilkudziesięciu godzin dla materiałów o niższej odporności do kilku tysięcy godzin dla materiałów wysokoodpornych.
Czy test AASS nadaje się do wszystkich materiałów?
Nie, test AASS jest szczególnie agresywny i nie nadaje się do badania stali zwykłej, stali ocynkowanej czy odlewów aluminiowych. Jest dedykowany głównie dla materiałów o wysokiej odporności korozyjnej.
Jakie są koszty przeprowadzenia testu AASS?
Koszty zależą od liczby próbek, czasu ekspozycji i zakresu analiz. Inwestycja w badania korozyjne zwraca się poprzez zwiększenie trwałości konstrukcji i redukcję kosztów konserwacji.
Czy wyniki testu AASS można bezpośrednio przełożyć na warunki rzeczywiste?
Test AASS to badanie przyspieszone, które symuluje ekstremalne warunki. Wyniki wymagają interpretacji przez specjalistów i przeliczenia na rzeczywiste warunki eksploatacji.
Jak często należy powtarzać badania odporności korozyjnej?
Dla nowych materiałów badania wykonuje się na etapie rozwoju i certyfikacji. W przypadku konstrukcji eksploatowanych zaleca się kontrole co 2-10 lat, w zależności od warunków eksploatacji.
Test AASS stanowi nieocenione narzędzie w arsenale inżynierów odpowiedzialnych za trwałość i bezpieczeństwo konstrukcji. Właściwe wykorzystanie tej metody badawczej pozwala na świadome podejmowanie decyzji projektowych i eksploatacyjnych, co przekłada się na zwiększenie żywotności konstrukcji i bezpieczeństwo użytkowników. W erze rosnących wymagań dotyczących trwałości i zrównoważonego rozwoju, badania odporności korozyjnej stają się elementem odpowiedzialnego projektowania i eksploatacji obiektów budowlanych.
Artykuł promocyjny